Mantenimiento de flotas mixtas: Jugar a lo seguro podría costarle dinero
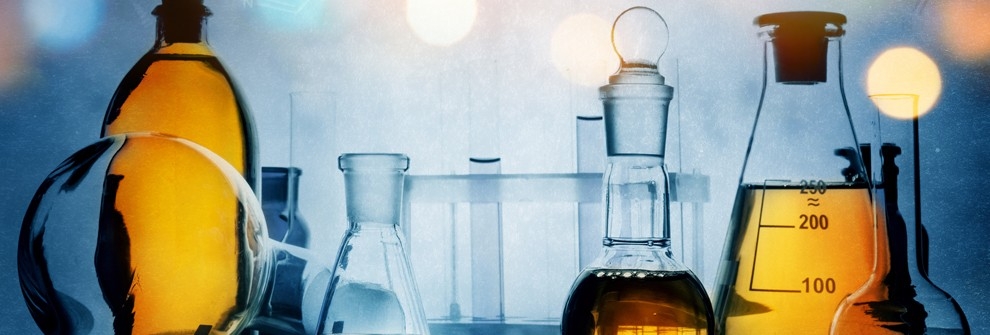
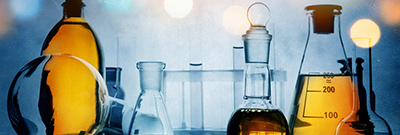
En conversaciones realizadas con los gerentes de mantenimiento de equipos de construcción, es claro que las flotas mixtas se han convertido en la norma. La mayoría mencionan las presiones que tienen de costos internos y la variabilidad en la calidad del equipo entre las compañías, como las principales razones por las que ya no son leales a un solo fabricante.
Si bien es cierto que las flotas mixtas pueden reducir los costos y a veces mejorar el rendimiento, existen contrapartes, una de ellas es un programa de mantenimiento intensamente más complicado. Diferentes OEM (fabricantes de equipos originales) tienen otras especificaciones de intervalo de servicio y mantenimiento, distintos requisitos y otras necesidades de lubricantes, lo que hace que el mantenimiento sea un acto de malabarismo difícil.
¿Cómo se las arregla con esto? Muchos gerentes adoptan un enfoque conservador para los programas de mantenimiento y los intervalos de drenaje de aceite, tratando de encontrar un común denominador que funcione en toda la flota. Sin embargo, esto da como resultado que la programación del servicio y los cambios de aceite se realicen con más frecuencia de la necesaria y por debajo de las recomendaciones del OEM. Este programa conservador, de acuerdo al razonamiento, es una "póliza de seguro" barata que creen que eliminará la necesidad de un análisis periódico del aceite.
Lo que estos gerentes no entienden es que el análisis de aceite no se trata solo del aceite. A través de su análisis, se pueden identificar muchos tipos de problemas en su equipo: cómo detectar si hay reducción de combustible, contaminación por suciedad, fugas de refrigerante o algún otro problema que pueda deteriorar el rendimiento. El análisis de aceite lo ayuda a predecir y posiblemente a evitar fallas inesperadas del equipo.
Establecer un programa de mantenimiento igual en toda su flota y eliminar el análisis de aceite puede aumentar los costos de material y mano de obra, al tiempo que aumenta hasta el 11% el riesgo de fallas catastróficas de una máquina en particular. Considere una pieza de equipo común, como una excavadora de tierra. Los cambios de aceite, incluido el costo y el gasto del mismo, los filtros y la mano de obra, suman alrededor de $1,540 al año.
Suponiendo que su flota tenga 100 máquinas similares que reciben servicio de aceite cuatro veces al año, estaría gastando $154,000 al año en cambios de lubricantes. Al realizar un análisis de aceite regularmente, podría eliminar en promedio, al menos, un cambio de aceite por máquina cada año. En otras palabras, sin un análisis regular del aceite, usted gasta $38,500 más anualmente, de lo que necesita. Y eso sin tener en cuenta el tiempo de inactividad que puede ser significativamente mayor que el ahorro de costos de material.
Without regular oil analysis, you also reduce the ability to predict common equipment failures. For example, 40% of engine failures are related to cooling system contamination, which an oil analysis can detect. What’s the typical cost to replace or rebuild an engine damaged by coolant? Let’s say on average its $90,000. Conservatively, let’s figure one unexpected rebuild per year at $90,000. Add that to the $38,500, and that “cheap insurance policy” is costing roughly $130,000 a year.
Sin un análisis de aceite regular, también se reduce la capacidad de predecir fallas comunes en los equipos. Por ejemplo, el 40% de las fallas del motor están relacionadas con la contaminación del sistema de enfriamiento, las cuales se pueden detectar con un análisis de aceite.
Un programa integral de mantenimiento preventivo que le permita realizar un seguimiento fácil de todos los intervalos requeridos por el OEM; programar el mantenimiento apropiadamente y que incluya un análisis regular de aceite, puede reducir el consumo de lubricante en un promedio de hasta el 25% además de dar como resultado una mayor disponibilidad y utilización del equipo. Se le puede dar servicio al equipo adecuado en el momento preciso y recibir alertas de posibles fallas antes de que ocurran. Esto no solo reducirá sus costos de material, sino que también optimizará la productividad y maximizará el retorno cada vehículo.
¿Cómo es el programa que tiene hoy en día comparado con el que le gustaría tener?
10/20/2017